SHANDONG HOHN GROUP: DREDGING FLOATING HOSES AND PIPE AND FLOATS EXPERT SINCE 1988! DEDICATED IN OFFSHORE CONSTRUCTION;DREDGING;MARINE SERVICE.
Marine fenders are kind of a safety barrier designed to protect ships, ports and people against impact forces. In simple words, it protects vessels and berth from damaging each other when they collide. This safety equipment acts as the interface between the ships, boats, berth, and floating platforms; thus providing much needed cushioning effect in between.
Made of materials such as foam, rubber or air filled within special elastomeric substances; they act much like a spring storing and releasing energy. Also called as marine bumpers these have to cope with the extreme forces under variable conditions. Whether its naval vessels, small boats, large docks or piers; marine fenders forms one of the key marine equipment for safe marine operations.
The port facilities have changed drastically in the past so does the ship’s with increase in maritime traffic. Modern ships used fixed marine fenders installed on their hulls; which protect them from hull damage in event of contact with another ship or berth. Sea piers and docks also utilize dedicated fenders of their own to minimize impact forces at the time of docking.
It’s Impact On Crew Safety & Safety Of The Ship
- There is a constant effect of tidal forces on ship’s, boats and floating terminals that push them even when they are idle.
- During berthing or ship to ship transfer it is these forces that cause the ship’s or boat to collide with each other.
- When two ship’s or boats collide even under the effect of just tidal forces.
- A huge amount of energy is transferred on impact of the two hull surfaces; that create a sudden change which become fatal for its crew much like what happens when the bus stop’s suddenly.
- Not just that hull collisions damages the ship’s structure and many equipment’s and many a time makes them unsuitable for next voyage.
- A marine fender protect us from these negative consequences by acting as a cushion in between the two ship’s or boats.
- It absorbs the forces in case of impact and thus reduces its negative effect on ship’s crew and its machinery.

Basic Features of Marine Fenders
- Safe & Reliable: Almost all fenders are constructed of layers of strong material that can withstand high pressure and cutting. To ensure high operational safety and reliability; they are pressure tested in controlled condition under various percentage of compression.
- Does Not Deteriorate: Modern marine fenders utilize the elasticity of compression found in air and foam and thus does not deteriorate much with the passage of time. This ensures its performance remains the same as it used to when brand new.
- Cost Effective: Made from elastic material that does not deform, degrade and withstand extreme pressure; they last long and does not need maintenance. This all add up to its low operational cost and better overall efficiency. Having simple design and low cost installation also go in favor of its cost effectiveness.
- Is Adaptable To Tides: Filled with foam and air these fenders float on top of water in an unrestricted manner. It can move up and down as the tides increase or decrease. This make sure the fender is always is in appropriate same position relative to the ship’s hull.
- Produce Soft Reaction Force: Buoyant or fenders have to continuesly work under varying load conditions. Depending on the approach of the ship and angle the force can go high or extremely high. The best thing about marine fenders is that their reaction forces does not increase even when there is excessive load or impact pressure on them.
- Can Withstand Extreme Forces: A ship exert maximum force on a buoyant when it came to berth at an angle. While the energy absorption decrease drastically for traditional protection in the form of tires or cushions. But modern fenders are designed and made in a way that they perform well under all extremes.
It’s Classification Based On The Type of Material
There are various types of marine fenders developed overtime to cater specific needs; thus preventing loss to ship’s and berthing facilities. To keep-up with the increasing quality guidelines such as; best design, high performance, long life and low maintenance. Different types and sub types of fenders are developed over the time.The different types of fenders available in the market based on the type of material used are:
A ) Rubber Fenders
Rubber fenders are developed in different capacity and variations to meet with the specific requirements of; LNG platforms, ship’s, container berths, offshore terminals and other marine structures. They are build in compliance of the PIANC guidelines targeting specific application. These are of highest quality and in most demand for maritime applications.
A rubber fender provide excellent absorption capabilities for the reaction forces. They also helps guide the residual hull pressure along the angle; thus reducing the overall effect of impact or collision. Solid rubber fenders had been used for the purpose for years and has only become better with time.
Thanks to its high demand and need for adjustments with changing maritime needs. They have played a greater role in the development of rubber industry over the years. Almost all rubber fenders build today are unique in a way and serves a specific purpose. These sub-types of rubber fenders are classified down below:
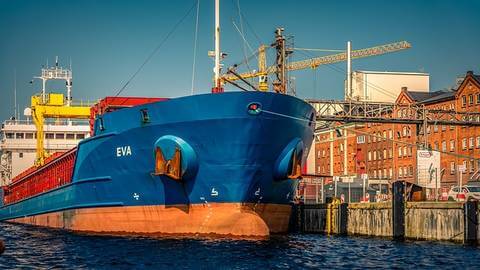
1 ) Arch Fenders
These are the special types of fenders used where the mounting space is limited; and to be used against small and mid sized ships or boats. They are simple in designs and provide better reaction forces at much lower cost. These V-Shaped fenders are easy to install and can work under the most severe conditions.This fender type was developed to improve the energy absorption capability for rubber fenders than its predecessor; such as the cylindrical fenders. Unlike older designs they can be installed with either face pads or with steel plates. Due to its low initial cost with little to zero maintenance requirement they are considered one of the best fender system to have.
These are reliable, easy to install, withstand rough sea conditions, have long service time and diverse in its application and installation ways. If used on the corners of the harbor they can also be termed as the corner arch fenders.
2 ) Cylindrical Fenders
These are the most basic types of the rubber fenders used today for maritime activities. They are simple in design, cost effective, versatile and per-requisite to the arch fenders. Available in three basic size; small, medium and large they can be used on all boats, ship’s, berths or stations. The best part is being quite easy to install and economical in nature.
Made with processes such as the compression molding they are homogeneous in nature, non porous and have thick wall. This provide some of its key characteristics such as; high abrasion resistance, simple yet robust design, progressive load deflection curve and better stress accommodation.
These simplest rubber fender type can be installed with chains, supporting bars, brackets and ladders. It provide low pressure and reaction forces to hull and can be installed both horizontally or vertically.
3 ) Parallel Motion Fenders
The parallel motion fenders is a next level of fender system that utilize modern technology to provide; a 60% higher absorption capabilities without affecting the resultant forces. This increase the capabilities of the berth drastically allowing it to dock larger ships and boats for the same working space.
They are made in a way it is at complete advantage in respect to conventional fenders. It can easily cope with large berthing angles, higher impact load, lower reaction forces, even distribution of forces and feature a non tilt frontal panel. The complete unit is divided into three main parts; frontal steel panel, a turning lever and back structure.The turning lever is mounted in between the frontal steel plate and back structure. In event of impact this lever restrict the movement of frontal steel plate other than moving parallel to the mounting. This allows for same performance and control irrespective of the berthing angle.
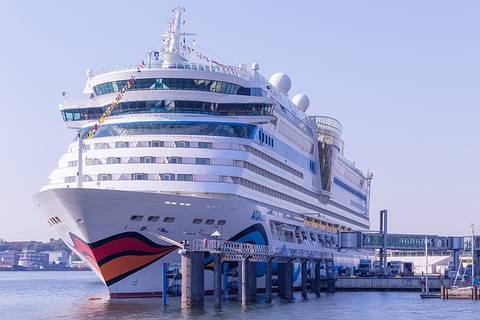
4 ) Cell Fenders
Cell fenders are among one of the most used rubber fender in the maritime industry. Its simplicity, easy to installation, strength and high performance has made a solid performance record. Available in variety of shapes and size they are capable of supporting both small and large vessels with minimum reaction force.
The key feature of this design is that it can be used for vessels with low hull design. Furthermore they can be used alone, as a pair or in multiple combinations. It consists of a rubber embedded flange mounted on a hollow cylindrical body. Together they deflect as much as 50% of forces in axial direction.
It’s a robust design that being tried and tested for the last 40 years. It offers high energy to weight ratio and is a cost effective solution to the modern parallel motion fenders. Since it show lowest variation in its compression performance it show same results regardless of weight of the vessels.
5 ) Leg Fenders
A combination of both worlds design and performance; its light and easy to install thanks to its modular design. It is installed where you need to have high performance under restricted space. Constructed of three parts “leg pairs”,”facing pads” and “fenders with steel panels” these are compact and versatile.
The biggest quality of these rubber fender type is that; its legs can be combined together to form a larger modular fender system. Being able to be installed both vertically and horizontally; they are flexible and versatile ensuring lower reaction and better energy absorption. These are used mainly at the berthing stations that deals mainly with larger ship’s.
Due to lower working parts resistant to wear, heat and shear load they are maintenance free and are thus cheap. Used in places such as container quays, tanker terminals, fender piles, Ro-Ro and bulk cargo berths.
6 ) Super Cone Fenders
It is the most modern design of rubber fender build upon the technology of cell fenders. So in a way one can say its the third generation of the cell fenders. They are known for their optimum performance, better efficiency, higher stability and better performance under shear and compression loads.
Its unique cone shape structure gave its name and keeps it stable even at higher angle of impact or compression. It also leads to have increased absorption, better performance and longer service life. Being the most modern of all marine fenders type, it allows to have same results with lesser fenders installed.
This leads to better overall efficiency, lower need for maintenance and thus lesser operational cost. They are made in away that can be used for a variety of applications and under varying conditions.
7 ) Slide In Slide Out Fenders
Developed to meet the requirements of multipurpose terminals these are easy to install and maintain. It’s design is quite straightforward with wear pads bolted onto the frontal panel. Such arrangement significantly reduce the time needed for maintenance work. For example in case of a failure; we now not need to change the complete assembly but just the wear pads.
Even the sliding panels can be easily replaceable with the guiding rails; thus reducing the safety risk associated with the maintenance activity. This allows for faster operation and zero delay due to fenders issues; all you need to do is to lift out the sliding panel and insert the replacement or spare panel.
Overall its an excellent fender system that that posses all the major advantages of traditional fender system; with a much better maintenance capability and cost of operation.

8 ) Pneumatic Marine Fenders
Have you seen those large rubber cylindrical blocks floating on water with many a times tires attached all around them? If you had anything to do with maritime activity you must have seen it once. These are the most idle fender type used for almost all ship to ship transfer and majority of port activity.
Thanks to them the risk of damage to the ship and its crew is reduced significantly while mooring operations. It is made up of thick layer of vulcanized rubber with end flanges to charge in air. They also posses a network of tires attached to their outer surface through a series of chain connected to its body.
The main advantage of using pneumatic fenders is that it can withstand and absorb; forces generated by inclined berthing at oblique angle, is relatively safe, adaptable to tides, is strong against high shear forces and does not deteriorate over time. Easy to deploy and fast application made it one of the most used types of rubber fender.
9 ) Extruded Marine Fenders
Available in “D” and “Square” shape they are used when you require a multi-purpose berthing solution for small ships and boats. They are known for their robust design and flexibility to cover any surfaces even curves. They are directly fastened onto the surfaces using bolts and require little to no maintenance during their lifetime.
While it absorbs the minimum forces of all rubber fender types its only advantage is its simple design and wide range of custom size. Made of NR/SBR rubber compound they are highly abrasive but resistant to UV and shear forces. They are typically used for pontoons, tugboats, jetties and in inland waterways.
B ) Foam Fenders
Idle for most ship to ship transfer its a dual layer closed cell structure; with high quality polyethylene foam to the core with a tough Polyurethane skin. Polyurethane is used for the purpose because its better than rubber in terms of; specific gravity, friction, durability, better compatibility with foams and absorption of impact forces.
Its design is so robust that no matter how badly it is abused it will never soak in water or burst. The best part is you can use it for its lifetime and still reuse the foam inside for producing another fender. So it pretty much retain much of its value even when its damaged or completed its lifetime.
The advantage of having a high density foam filled inside a thick skin of polyurethane is that; its outer layer is water and wear resistant while the inner foam makes it have lower reaction to compression ratio. Its design makes it unsinkable, easy to install, rapid response and fully customizable; as you can simply change its performance by changing the type of foam inside.
Application wise thanks to their flexibility in abilities with compression and reaction forces; they can be used with different settings with ships and boats of different size and weight. Based on their particular application and characteristics they can be classified into following three types:
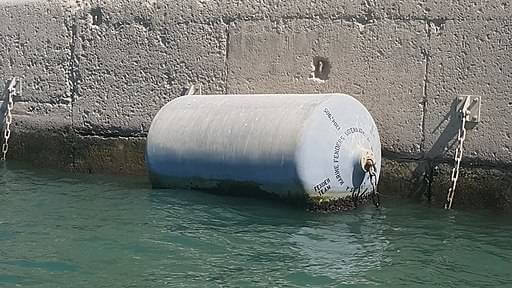
1 ) Sea-Guard Fenders
An alternative to the pneumatic rubber fender with a difference of using foam instead of air for the purpose. It consists of closed cell resilient foam at its core with a thick rubber skin on top. In many designs they also contain enforced nylon filaments in between the two. All the tires are then mounted on a chain net made of stainless steel.
Using closed cell foam technology ensures its unsinkable, high energy to reaction ratio and burst resistant. While using the thick rubber with enforced nylon filaments; makes it wear resistant, strongly reinforced, nondestructive, u.v protected and compliant with US Navy specifications.
Used mainly for ship to ship transfer when we need non deflecting, non destructible affordable fender system. These can be used as both suspended or floating type and require zero maintenance at all.
2 ) Sea-Cushion Fenders
Introduced first in 1974 sea cushion fender was one one its kind with foam filled inside. They soon being recognized as the rough and tough fender type; the one with higher performance and better reliability. Designed to do the heavy lifting in fender industry they are used mainly for heavy and bigger ships.
Much superior to its counterpart Sea-guard fenders these have a network of chain tire on them; which acts both as an extra cushioning and protection. Since being filled with foam they can not burst and thus used largely for LNG tankers. They bring in extra security, low reaction high energy option in a robust light design.
Available in wide variety of diameter and lengths its used throught the world in variety of applications. The major advantage of using this type over other is; its cost effectiveness, longer service life, similar performance even when punctured, large standoff distance, easy installation and adjustable to tides.
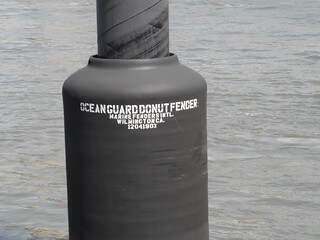
3 ) Donut Marine Fenders
This Marine fenders type is rather special that floats freely around a circular pile or pipe to follow change in water level. Other than typical marine fenders type its main job is to guide the ships while berthing at lock entrances and turning structures. It helps vessels to turn and slide along for proper alignment.
Made of reinforced elastomeric skin with a closed cell linked foam core it provide; lower friction, less shear forces and maintenance free self regulating structure. Easy to install, its unsinkable and provide high energy absorption thus protecting ship and increasing self life. Thanks to the low friction guides and up and down movement with tides it assist better to align the ships.
Generally these foam fender type are build with extra reserve buoyancy but; some designs also contains specialized buoyant chambers for the purpose. The biggest difference between them and the others is that here only one side is working under compression.
C ) Composite Fenders
Composite fenders or Rubbylene are constructed of the composite rubber profiles with a UHMW-PE coating. Together they provide low coefficient of friction and excellent wear resistance. Unlike other rubber fenders type the two material is not joined mechanically but rather; using the vulcanization technique.
These fenders themselves can be found in three main types; block composite fender, trapezium composite fender and keyhole composite fender. They can be mounted on the U-Beam or between the two stripes with mounting holes made on the sides of the fenders. This provide a resilient rubber body with lower shear forces.
These are used when you require to withstand the heaviest of ship’s and impact with high wear resistance. The combination of UHMW-PE and natural rubber allows it to be great product with unique characteristics. Its tough, versatile and durable with excellent energy absorption capacity for its size.
Conclusion
When a boat or ship berth or came in contact with one another; there is huge transfer of kinetic energy between the two. If remained unchecked these forces can break and damage the ship’s hull, dock and associated machinery. In larger context there will be acute damage to the crew and maritime infrastructure.
HOHN Marine fenders installed on ships, berthing station, boats and maritime platforms acts as a bumper; that absorbs much of that kinetic energy produced thus ensuring safety of life and money. It not just absorbs the shock and kinetic energy; but also redistributes the reaction forces to a minimum.
These marine fenders used can be of various types; rubber, foam or composite. Installed on boats, ships and dock station they protect the hull at ship’s head and side. In event of ship to ship transfer these fenders are placed at equal distance in between the two ship’s. Overall they are robust, easy to use, wear resistant and with the ability to absorb most energy.
Please contact our engineers team for more details: www.floatinghosesllc.com